
- Setting up sheetcam for a homemade plasma cutter how to#
- Setting up sheetcam for a homemade plasma cutter pdf#
The sleeve was installed quite differently because the time was running out and no welds could have been made at the time. The X-movement was achieved using the same trapezoidal screw as in Y-axis and similar bearing support was used at the other end. The Y trapedzoidal screw was welded to a 3 mm thick metal plate which was later on bolted to the Y-sled: It has 2 V-groove bearings on either side of the sled and two more on the vertical line to hold the weight of the Z-axis and such: The Y-sled was constructed from a custom bent steel profile with a material thickness of 2 mm. The flexible coupling allows to have radial movement and thus avoids carrying over some vibrations if the trapezoidal screw isn't absolutely straight. The Y-movement was achieved by using a M16 trapezoidal screw where the ends of the screw were cut to 12 mm OD using a lathe to fit the flexible coupling for the stepper motor, and bearing support at the other end. The Y-rail needs some reinforcement to avoid flexing between the sleds, so some 22 mm OD pipe is used and 6 mm holes are drilled to the U-profiles and 6 mm threaded rod is used with nuts to tighten them together: The X-axis movement was built using 1 m long trapezoidal screw with flex coupling on the motor end and a support bearing at the other end: A 10 mm threaded rod is used again with M10 nuts to tighten the whole assembly together.

Some 10 mm holes need to be drilled to the U-profiles so that the Y-rail can be attached as seen from the first picture. The bearings used were 630VV-V groove bearings that are available from ebay and ali-express. Some boltscrews were used to have low profile for the assembly as seen from the photo below.
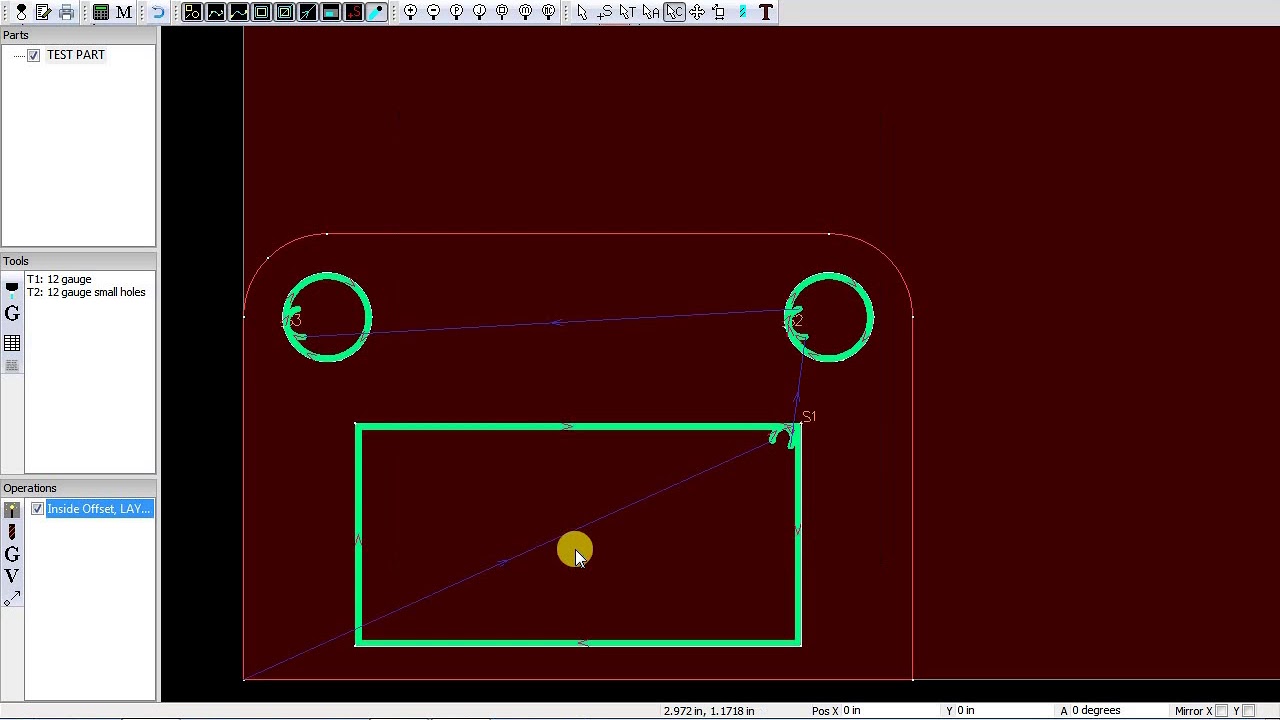
The U-shaped profiles are set on top of each other to have clamping effect for the bearings, so that the tightness can be adjusted. First model was build using 2 bearings on top and one at the bottom, but it was found out that 2 at top and 2 at bottom makes the rig more rigid. The frame rails are used as guides, so next up using some U-shaped profiles and V-groove bearings were used to create sleds. The longer rails are easy to set at 45 degree angle when the Y-axis cross rail has been cut to length. And using some 10 mm threaded rod the rails were joined to the metal L-frames. And the frame rails were attached together using some L-shaped 4 mm thick metal reinforcements from a hardware shop that had a symmetrical holes cut to it. Final dimensions of the frame were 670x1000 mm. The frame was built using general furniture square steel with dimensions of 40x40x1.5 mm.

Setting up sheetcam for a homemade plasma cutter pdf#
PDF files and are on CDs with constructions pictures.
Setting up sheetcam for a homemade plasma cutter how to#
Included are informational videos showing how to set up and use SheetCam for parts placement and cutting order. The cost for building this table is about $1300. Including wiring diagrams for motor circuits and computer connections, construction of floating head torch mount and water table. Complete parts list with vender for bearings, electronics, and drive components. tap files for cutting parts the rest are standard steel angle and square tubing.

Basic plans are for a 4’ X 4’ cutting area but can be easily changed to a larger or smaller table. The plans cover a complete construction of a CNC table that can be used for plasma, routing, and light milling of aluminum parts.
